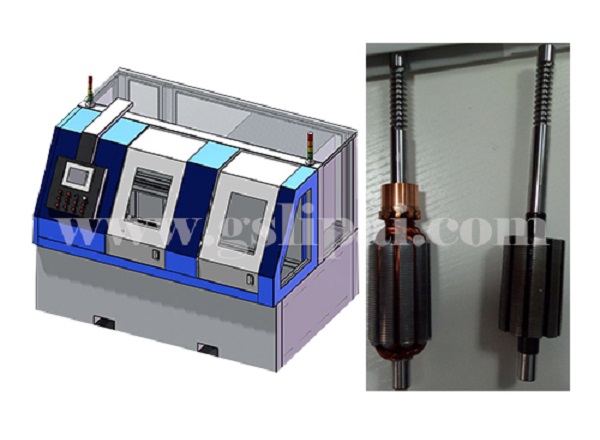
When the precision motor is running normally, the type of mechanical equipment force and torque that the shaft bears varies with the type of motor and the transmission mechanism. The key forces are: the gravity of the rotor assembly itself, the one-way magnetic resistance caused by the eccentricity of the rotor, the centrifugal force of the unbalanced total weight, the load torque of the shaft extension end on the shaft by the function of the transmission mechanical equipment, etc. Therefore, the shaft of the motor must have sufficient compressive strength to avoid residual deformation or damage to the shaft during the working state and production process of the motor. The surface hardness standard has a certain degree of assembly interference in the manufacturing process, and the shaft hardness standard also has strict requirements.
The precision motor shaft quenching machine we designed for Indian customers has satisfactorily completed the customer’s use requirements.
1. customer workpiece requirements: the depth of the effective hardened layer of the workpiece is ≥ 1.2mm
2. customer workpiece material: 45 steel, SCM440H, followed by 40Cr, SCM440C, GCr15.
3. customer capacity requirements: 50,000-60,000 pieces/month
Our product advantages
1. The automated precision quenching machine tool we designed can be connected to high-frequency quenching equipment and other related machining equipment (reserved electrical communication port for automatic loading and unloading), which can be used to form an automatic wire body to realize machining (roughing before high frequency, semi-finishing, post-processing after high frequency heat treatment). One-stop processing of high-frequency heat treatment, and the equipment control system is equipped with an internal system (visualization platform) to collect data output ports.
2. Automatic loading and unloading mechanism. Before the high-frequency quenching machine tool, a manipulator can be used to grab and take materials. The quenching machine tool can be designed as an automatic door. The equipment has two control modes: automatic and manual control. During the debugging stage, the manual mode can be used for debugging. , after the debugging is completed, it will be converted into automatic unmanned mode operation.
3. The machine tool control system adopts Siemens 8080D configuration, the repeatability of the machine tool is 0.05≧mm, the coaxiality of the upper and lower centers is 0.1mm≥, and the spindle speed is not less than 0-150 (rpm/min).
4. There are comprehensive mechanical and electrical interlocking protection devices in the control system, and three-color lights are set to clarify the working status of the equipment and facilitate on-site management.